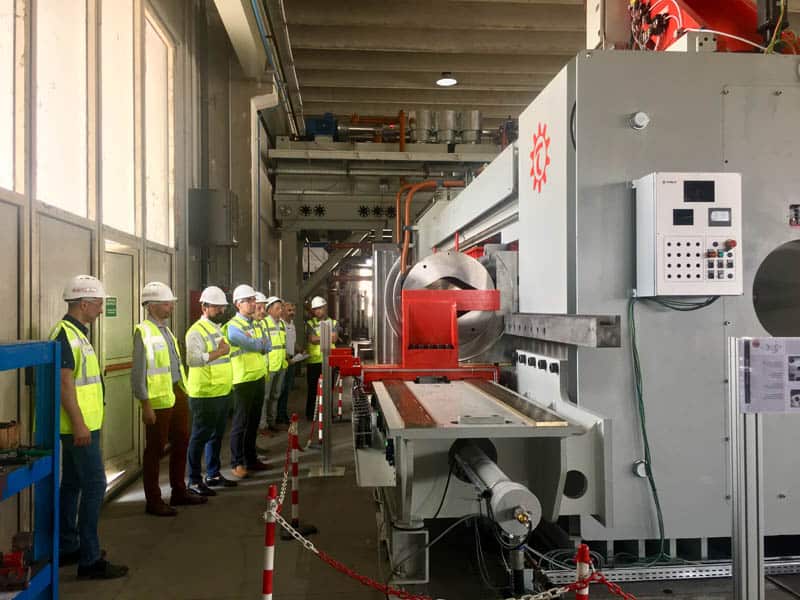
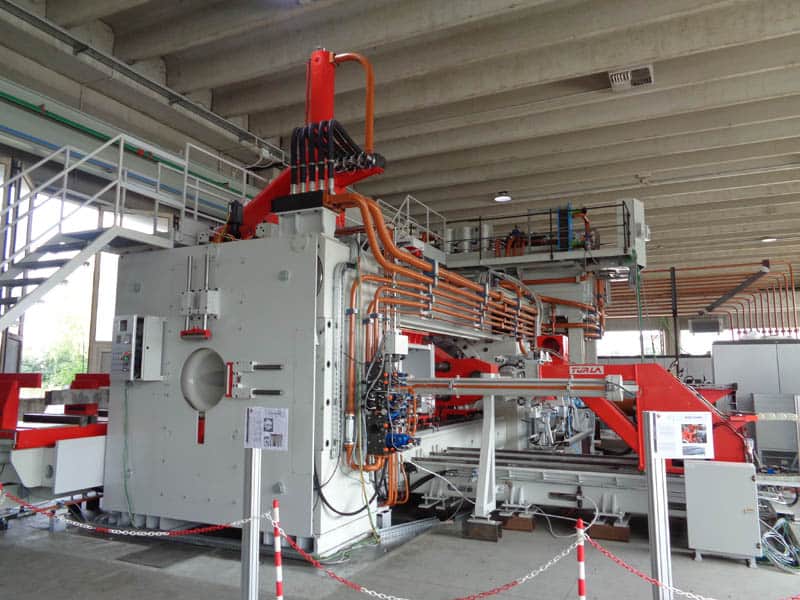
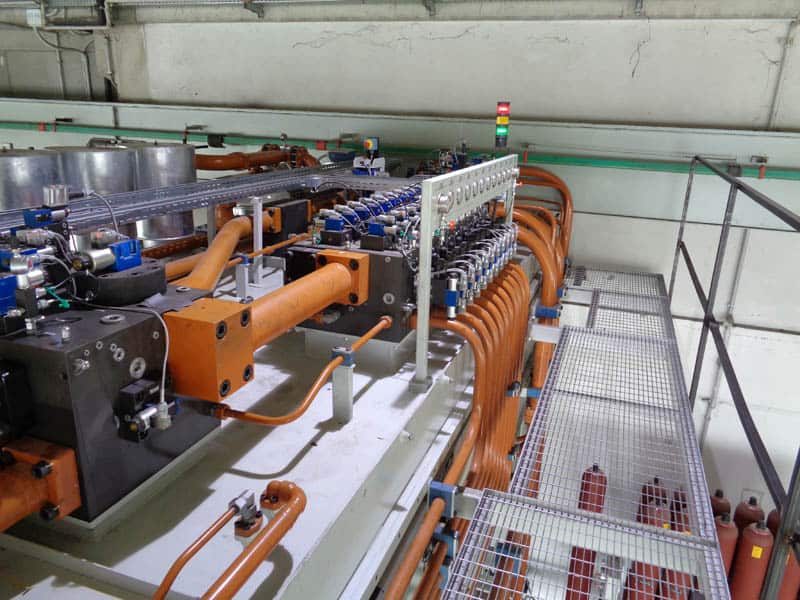
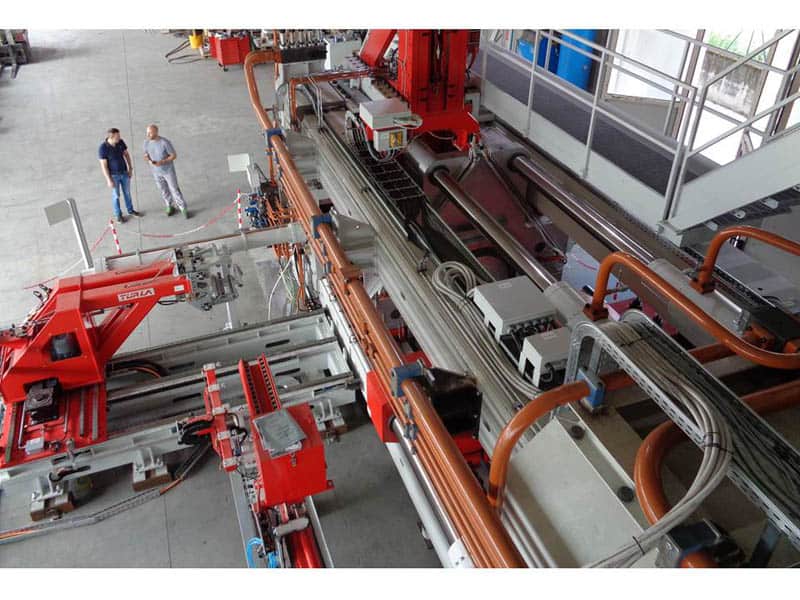
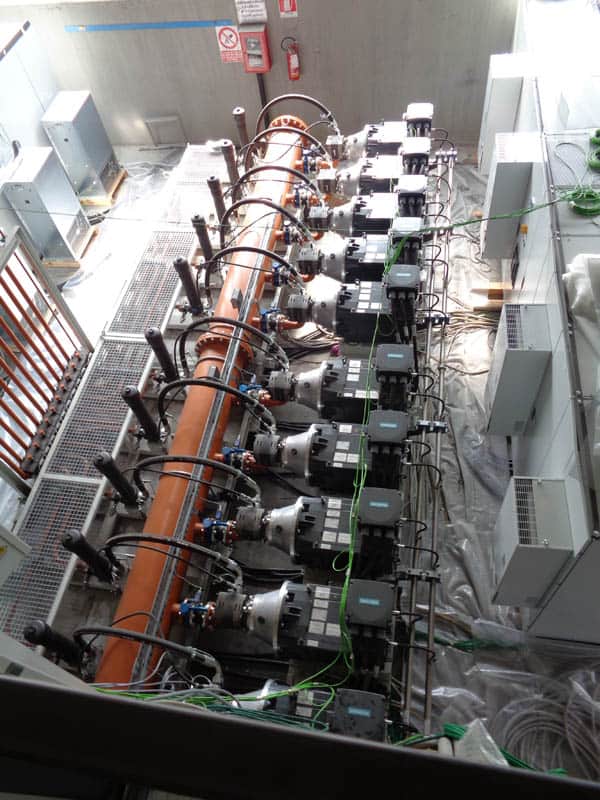
Two major extruders in Spain—INALSA Group and Extruidos del Aluminio S.A EXTRUAL)—are expanding their operations. The companies have each placed orders for Turla 50 MN extrusion lines, which will enable them to grow their market presence both within the country and internationally.
According to their history and philosophy throughout the years, both extruders have developed their own strategies to become important players serving markets such as industrial, automotive, trailers, and railway, among others. The choice of the press was a main challenge for both companies. Having a press with the most modern features in terms of force control, accurate alignment, correct billet containment, optimal container heating, and minimal platen deflection would be absolutely necessary to pro-duce such difficult profiles. Both extrusion systems will be designed and manufactured to include Turla STeP5 gas ovens, the new presses will each be installed with Turla’s Eco+Logic 2.0 system, which will be able to reduce energy consumption, an important concern for the extruders. For EXTRUAL, it was also important to have flexibility in the production process. “Machines must be designed to guarantee a fast tooling change that minimizes the downtime in case of frequent changes of production.” explained J.H. Leal, factory manager for EXTRUAL. At the same time, INALSA’s technical team focused on traceability within the system. They wanted to have the ability to understand the story of every billet since it guarantees full process control and provides a process record and they highly appreciated the ability of Turla’s recipe system to store the data for every machine so that data can be retrieved very easily and can be improved if necessary, thanks to the PLC control and the accuracy of control systems that permit the immediate implementation of the best working conditions.